I’m working on a commision that calls for a moulding on both the front and sides of the same piece. The profile is a Cyma recta. I’ve had this moulding plane for a number of years. I haven’t sharpened it in a long time, and I’ll tell you why: sharpening risks changing the profile on the iron. If you do this, you will need to rework the sole profile. However, because it had been a year since I sharpened it last, I worked the profile using a combination of waterstones.

These are the three primary stone I reserve for my entire set of moulding planes. When sharpening, I spend no more time than necessary, which is about 5 minutes. Because of the hollow grind in the centre of the profile, it takes so little time. Yes, you’re probably surprised to learn that, and I believe I’m the only person in history to use a hollow grind in moulding plane irons. I did it by running a dremel through the middle without touching the profile. It doesn’t take long with such a small amount of material to sharpen. It’s similar to adding a secondary bevel, which I strongly advise against doing on a moulding plane. If you do, you will have so much material to remove that you will almost certainly have to change the profile. The frequency with which I use this plane will determine how frequently I need to return to the stone. Because most of my work does not require mouldings, I won’t need to return for a while, but for now, all I need to do is lay the iron on its back on the stone and give it a few strokes from 1000 grit to 8000 grit, followed by lapping the profile on the strop. She’ll be very sharp, and you didn’t take the risk of changing the profile.



As you can see, there isn’t much to get rid of. After that, I run it through a few laps on my strop, and she’s ready to take shavings. I usually use the finger nail test to check for sharpness, but I wanted to show you how sharp it is after only 5 minutes of sharpening and before I went to the strop. Here’s a quick video of me creating mouldings.



As lovely as the end grain appears, profiling the two sides took a long time. It not only prematurely blunts the blade, but it is also extremely difficult to plane. After that, there’s a lot of sanding, but sometimes you don’t have a choice, like I didn’t, and you have to do what you have to do. This is how I do it:
I leave the width wider than necessary so that when I break out on the ends, it won’t matter because I’ll saw it off and plane it to width. I then make dadoes first, and then plane the front profile. This is how I hand plane a moulding, and the results speak for themselves.
Now for the confession: I’m not a big fan of using complex moulding planes; I’d rather use hollows and rounds because there’s less chance of changing the profile when sharpening. While it is true that any hollow or round profile can be changed, a simple profile is easier to fix than a complex profile. It’s fine for one-time use, but it’s an unnecessary risk for regular use.
A router may be faster, but it is sweeter and quieter to do it by hand. It still amazes me, as along as I have worked wood by hand, that I still get that buzz everytime I complete a project that I did it by hand.
Another brilliant idea is to make kerfing planes out of disposable saws. It may come as a surprise to you, but it actually makes sense. You’ll need to buy the saw plate first, then if you’re lucky enough to have a tooth punch, you’ll be halfway there, but if not, you’ll have to file the teeth and go through a lot of expensive saw files. Still, for those with a sizable bank balance and the know-how, all of this is tolerable. What about those who don’t know how to file teeth on saws or sharpen one? In this case, I believe that purchasing a disposable saw from your local hardware store is a better option.
I’m going to make a kerfing plane soon because I believe it’s absolutely necessary if you’re resawing by hand with a Robou saw or just a handsaw. I believe it will not only help you with accurate resawing but will also shorten the time it takes to resaw a board. Now, I’m lucky enough, a friend of mine filed the teeth using Isaac Blackburn’s version on an old saw he had.


I like this version better than the saw type.
What is one to do when there is only a small amount of material to remove, and it is too small to saw and too tedious to shoot due to its thickness and tough end grain?

With your block plane, knock off the edges, leaving only a small amount of material to shoot.

Now when you shoot it won’t be as tedious nor strenuous. The end grain will be easy to shoot as if its been moistened with alcohol or turps, mineral spirits etc. I hope this was helpful.


I’m guessing the concept was taken from worksharp. Having said that, I’m not sure how effective this method would be. There would have to be some level of downward pressure if you were to sharpen effectively, and I can’t see being stable. Maybe I’m wrong, but unless someone knows differently, I’m none the wiser.
I found this video on FB and I edited the part of interest only. Have you seen this method before? Because I have not. I think this is a great temporary solution until one can afford a proper sawmill.
This is a short video on the method and planes I use to take a hump out of a board.

This one is a definite must in every shop!



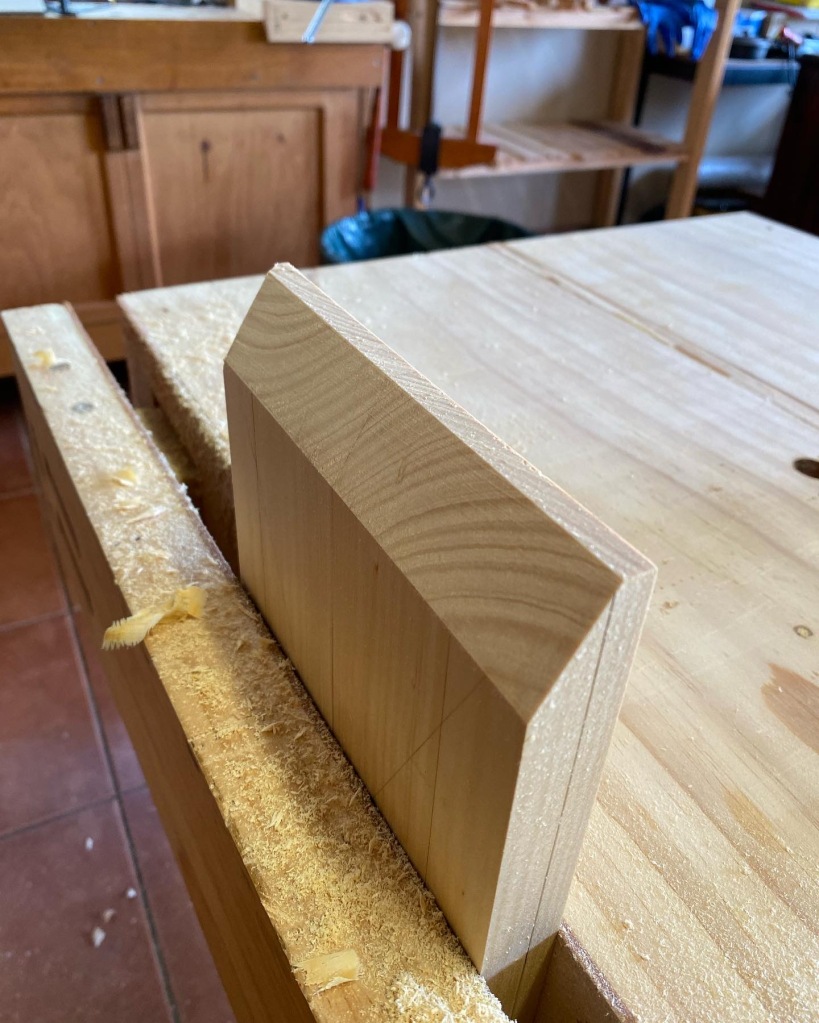
Raising a panel with straight bevelled edges is a simple and uncomplicated task. More than that becomes tiring, but it isn’t difficult. Someone suggested that you skew the plane to 45° to avoid breaking out the ends. It is incorrect to assign a specific angle to this. Any angle will lessen the impact of spelching, but will not completely eliminate it. If you want to feather the edges or belly the panel, you can angle the plane, but if you want the edge closest to the panel to be crisp and straight, the plane should not be angled. Of course, severe spelching will occur, but this can be avoided by chamfering the edge. Another thing that comes to mind, and I should have mentioned it first, is to saw off as much of the waste as possible before planing. This will save you a lot of time, and if you lose concentration like I did, you will go over your line, and the amount you went over the line will determine whether or not it’s game over.
If you’re a hobbyist like most people, completing one-time tasks, no matter how difficult, is a pleasurable experience. It’s also very cost-effective because no expensive machinery is required to do the work for you.
If I may get off the topic, I’d like to emphasise one very important point to which I adhere religiously. If you run a business and claim to work by hand, then you should. Whether you have one or fifty panels to raise, charge accordingly. It makes my stomach turn to see people use machinery and then claim it’s handmade. They are not only deceiving themselves and doing a disservice to themselves, but they are also doing a disservice to artisans who truly do all of their work by hand. They’re deceiving us because fewer and fewer potential customers believe you work entirely by hand, and it’s difficult to prove otherwise without inviting customers to your shop to witness this phenomenon for themselves.
[the_ad_placement id=”manual-placement”]